Assembly
Our assembly division is an essential part of our services, ensuring that the systems and equipment developed and manufactured are installed correctly and efficiently.
1. on-site assembly
Complete installation:
Carrying out the complete installation of environmental technology systems on site, including all necessary components and systems.
Commissioning:
Testing and commissioning of the systems to ensure that they function properly and meet the specific requirements.
2. modular design
Pre-assembled modules:
Production and pre-assembly of modules in the factory, which can be assembled into complete systems on site. This reduces installation time and minimises interruptions to the customer's operations.
Flexible customisation:
Customisation and integration of the modules according to the specific requirements and conditions at the installation site.
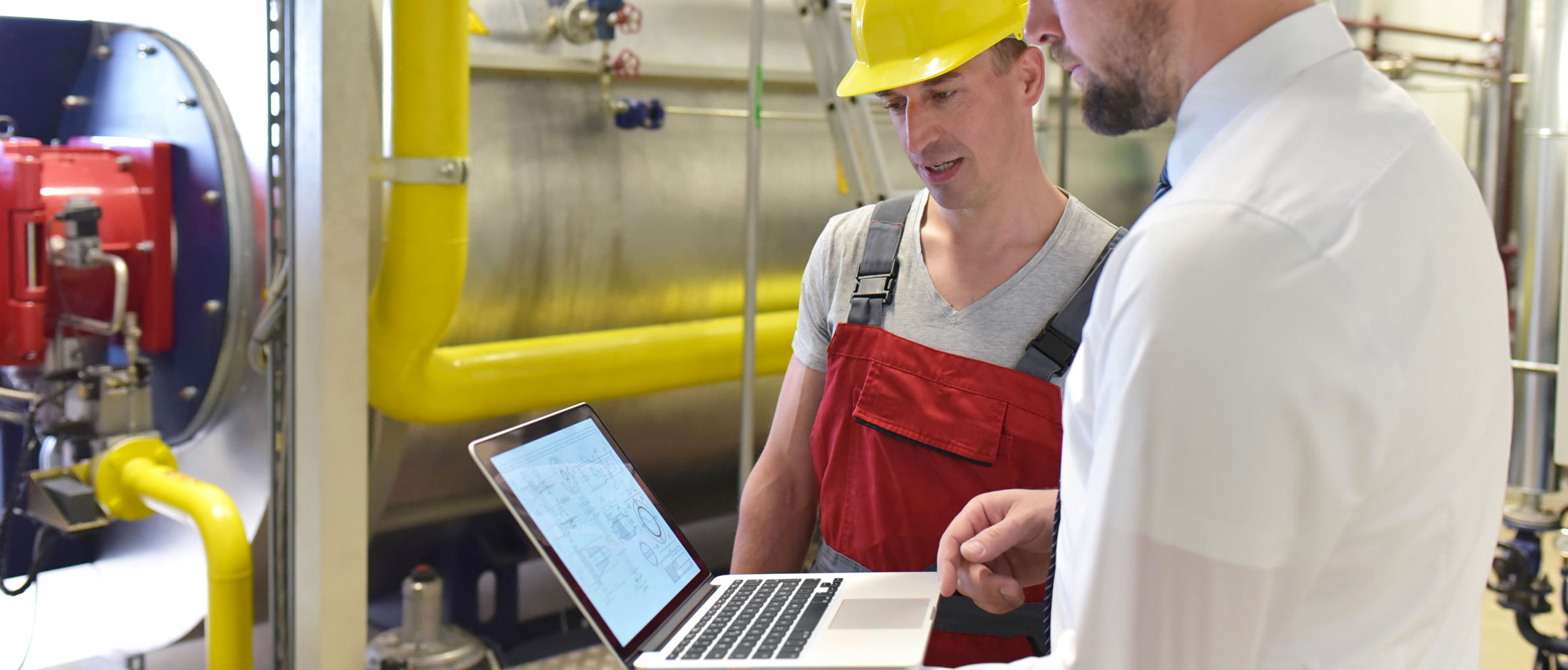
3. qualified assembly teams
Experienced professionals:
Deployment of highly qualified and experienced installation teams specially trained in LaCont technologies and products.
Safety standards:
Compliance with strict safety standards and regulations during assembly work to ensure the safety of employees and the environment.
4. technical support & consulting
Technical support:
Providing technical support and advice throughout the installation phase to ensure that all technical requirements are met.
Problem solution:
Quick and efficient solution to problems or challenges that arise during installation.
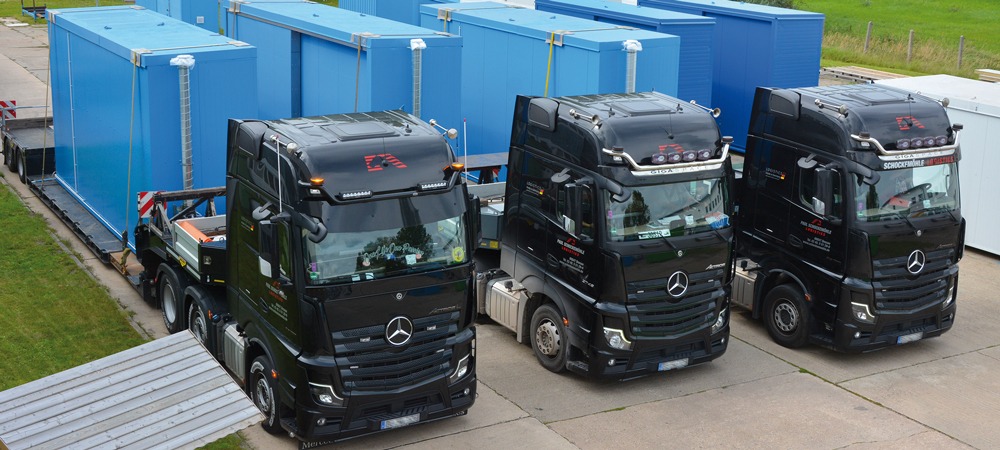
5. coordination and project management
Project planning:
Detailed planning and coordination of installation activities to ensure timely and efficient realisation.
Resource management:
Ensuring that all necessary resources, tools and materials are available for assembly.
6. sustainability
Environmentally friendly processes:
Use of environmentally friendly processes and techniques during assembly to minimise environmental impact.
Waste management:
Effective management and disposal of waste generated during assembly.
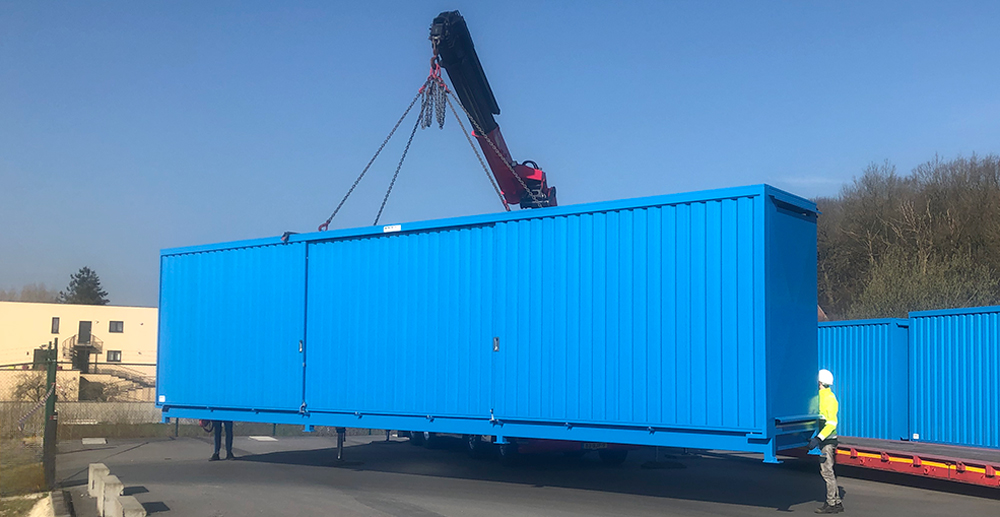
7. documentation and acceptance
Detailed documentation:
Preparation of comprehensive documentation of assembly activities, including technical reports and test protocols.
Acceptance procedure:
Carrying out acceptance inspections and tests to ensure that the systems meet the specified requirements and are ready for operation.
8. customer training and support
Training:
Training of customer personnel in the operation and maintenance of the installed systems to ensure optimum utilisation and long-term reliability.
After-sales support:
Provision of after-sales support and maintenance services to ensure the long-term operation and efficiency of the systems.
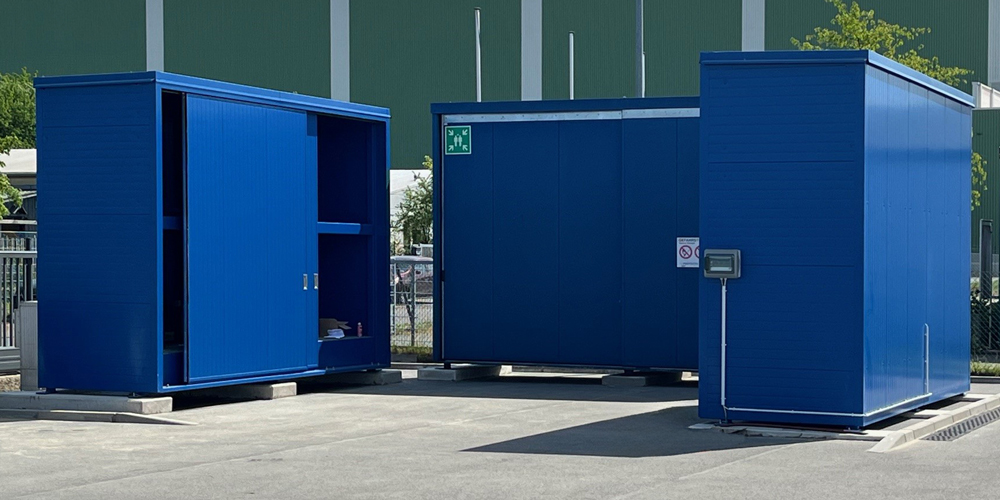